百科详情
发布时间:2022-03-04 21:51
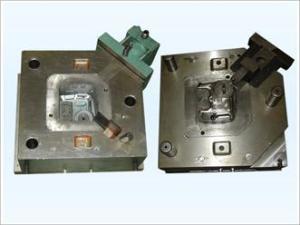
1压铸模具
压铸模具是压铸生产的三大要素,缺一不可。所谓压铸工艺就是将这三大要素有机地加以综合运用,使能稳定地有节奏地和高效地生产出外观、内在质量好的、尺寸符合图样或协议规定要求的合格铸件,甚至优质铸件。
2介绍
压铸模具是铸造液态模锻的一种方法, 一种在专用的压铸模锻机上完成的工艺。它的基本工艺过程是:金属液先低速或高速铸造充型进模具的型腔内,模具有活动的型腔面,它随着金属液的冷却过程加压锻造,既消除毛坯的缩孔缩松缺陷,也使毛坯的内部组织达到锻态的破碎晶粒。毛坯的综合机械性能得到显著的提高。[1]
3压铸模具合金
压铸件所采用的合金主要是有色合金,至于黑色金属(钢、铁等)由于模具材料等问题,目前较少使用。而有色合金压铸件中又以铝合金使用较广泛,锌合金次之。 下面简单介绍一下压铸有色金属的情况。
(1)、压铸有色合金的分类 受阻收缩 混合收缩 自由收缩 铅合金 -----0.2-0.3% 0.3-0.4% 0.4-0.5% 低熔点合金 锡合金 锌合金--------0.3-0.4% 0.4-0.6% 0.6-0.8% 铝硅系--0.3-0.5% 0.5-0.7% 0.7-0.9% 压铸有色合金 铝合金 铝铜系 铝镁系---0.5-0.7% 0.7-0.9% 0.9-1.1% 高熔点合金 铝锌系 镁合金----------0.5-0.7% 0.7-0.9% 0.9-1.1% 铜合金
(2)、各类压铸合金推荐的浇铸温度 合金种类 铸件平均壁厚≤3mm 铸件平均壁厚>3mm 结构简单 结构复杂 结构简单 结构复杂
铝合金 铝硅系 610-650℃ 640-680℃ 600-620℃ 610-650℃
铝铜系 630-660℃ 660-700℃ 600-640℃ 630-660℃
铝镁系 640-680℃ 660-700℃ 640-670℃ 650-690℃
铝锌系 590-620℃ 620-660℃ 580-620℃ 600-650℃
锌合金 420-440℃ 430-450℃ 400-420℃ 420-440℃
镁合金 640-680℃ 660-700℃ 640-670℃ 650-690℃
铜合金 普通黄铜 910-930℃ 940-980℃ 900-930℃ 900-950℃
硅黄铜 900-920℃ 930-970℃ 910-940℃ 910-940℃
* 注:①浇铸温度一般以保温炉的金属液的温度来计量。
②锌合金的浇铸温度不能超过450℃,以免晶粒粗大。
4压铸模具常见的问题
1).冷紋:
原因:熔汤前端的温度太低,相叠时有痕迹.
改善方法:
1.检查壁厚是否太薄(設計或制造) ,较薄的区域应直接充填.
2.检查形狀是否不易充填;距离太远、封閉区域(如鳍片(fin) 、凸起) 、被阻挡区域、圆角太小等均不易充填.並注意是否有肋点或冷点.
3.缩短充填时间.缩短充填时间的方法:…
4.改变充填模式.
5.提高模温的方法:…
6.提高熔汤温度.
7.检查合金成分.
8.加大逃气道可能有用.
9.加真空裝置可能有用.
2).裂痕:
原因:
1.收缩应力.
2.頂出或整缘时受力裂开.
改善方式:
1.加大圆角.
2.检查是否有热点.
3.增压时间改变(冷室机).
4.增加或缩短合模时间.
5.增加拔模角.
6.增加頂出銷.
7.检查模具是否有錯位、变形.
8.检查合金成分.
3).气孔:
原因:
1.空气夾杂在熔汤中.
2.气体的来源:熔解时、在料管中、在模具中、离型剂.
改善方法:
1.适当的慢速.
2.检查流道转弯是否圆滑,截面积是否渐減.
3.检查逃气道面积是否够大,是否有被阻塞,位置是否位於最后充填的地方.
4.检查离型剂是否噴太多,模温是否太低.
5.使用真空.
4).空蚀:
原因:因压力突然減小,使熔汤中的气体忽然膨胀,冲击模具,造成模具損伤.
改善方法:
流道截面积勿急遽变化.
5).缩孔:
原因:当金属由液态凝固为固态时所占的空间变小,若无金属补充便会形成缩孔.通常发生在较慢凝固处.
改善方法:
1.增加压力.
2.改变模具温度.局部冷却、噴离型剂、降低模温、.有时只是改变缩孔位置,而非消缩孔.
6).脫皮:
原因:1.充填模式不良,造成熔汤重叠.
2.模具变形,造成熔汤重叠.
3.夾杂氧化层.
改善方法:
1.提早切換为高速.
2.缩短充填时间.
3.改变充填模式,浇口位置,浇口速度.
4.检查模具強度是否足夠.
5.检查銷模裝置是否良好.
6.检查是否夾杂氧化层.
7).波紋:
原因:第一层熔汤在表面急遽冷却,第二层熔汤流過未能将第一层熔解,却又有足夠的融合,造成組织不同.
改善方法:
1.改善充填模式.
2.缩短充填时间.
8).流动不良产生的孔:
原因:熔汤流动太慢、或是太冷、或是充填模式不良,因此在凝固的金属接合处有孔.
改善方法:
1.同改善冷紋方法.
2.检查熔汤温度是否稳定.
3.检查模具温充是否稳定.
9).在分模面的孔:
原因:可能是缩孔或是气孔.
改善方法:
1.若是缩孔,減小浇口厚度或是溢流井进口厚度.
2.冷却浇口.
3.若是气孔,注意排气或捲气問题.
10).毛边:
原因:1.鎖模力不足.
2.模具合模不良.
3.模具強度不足.
4.熔汤温度太高.
11).缩陷:
原因:缩孔发生在压件表面下面.
改善方法:
1.同改善缩孔的方法.
2.局部冷却.
3.加热另一边.
12).积碳:
原因:离型剂或其他杂质积附在模具上.
改善方法:
1.减小离型剂喷洒量.
2.升高模温.
3.选择适合的离型剂.
4.使用软水稀釋离型剂.
13).冒泡:
原因:气体捲在铸件的表面下面.
改善方式:
1.減少捲气(同气孔).
2.冷却或防低模温.
14).粘模:
原因:
1.鋅积附在模具表面.
2.熔汤冲击模具,造成模面损坏.
改善方法:
1.降低模具温度.
2.降低划面粗糙度.
3.加大拔模角.
4.镀膜.
5.改变充填模式.
6.降低浇口速度
5压铸模具专业英语
landed plunger mold 有肩柱塞式模具
burnishing die 挤光模
landed positive mold 有肩全压式模具
button die 镶入式圆形凹模
loading shoe mold 料套式模具
center-gated mold 中心浇口式模具
loose detail mold 活零件模具
chill mold 冷硬用铸模
loose mold 活动式模具
clod hobbing 冷挤压制模
louvering die 百叶窗冲切模
composite dies 复合模具
manifold die 分歧管模具
counter punch 反凸模
modular mold 组合式模具
double stack mold 双层模具
multi-cavity mold 多模穴模具
electroformedmold 电铸成形模
multi-gate mold 复式浇口模具
expander die 扩径模
offswt bending die 双折冷弯模具
extrusion die 挤出模
palletizing die 叠层模
family mold 反套制品模具
plaster mold 石膏模
blank through dies 漏件式落料模
porous mold 通气性模具
duplicated cavity plate 复板模
positive mold 全压式模具
fantail die 扇尾形模具
pressure die 压紧模
fishtail die 鱼尾形模具
profile die 轮廓模
flash mold 溢料式模具
progressive die 顺序模
gypsum mold 石膏铸模
protable mold 手提式模具
hot-runner mold 热流道模具
prototype mold 雏形试验模具
ingot mold 钢锭模
punching die 落料模
lancing die 切口模
raising(embossing) 压花起伏成形
re-entrant mold 倒角式模具
sectional die 拼合模
runless injection mold 无流道冷料模具
sectional die 对合模具
segment mold 组合模
semi-positive mold 半全压式模具
shaper 定型模套
single cavity mold 单腔模具
solid forging die 整体锻模
split forging die 拼合锻模
split mold 双并式模具
sprueless mold 无注道残料模具
squeezing die 挤压模
stretch form die 拉伸成形模
sweeping mold 平刮铸模
swing die 振动模具
three plates mold 三片式模具
trimming die 切边模
unit mold 单元式模具
universal mold 通用模具
unscrewing mold 退扣式模具
yoke type die 轭型模
6压铸模具管理
一、目的 为使模具的验收、保管、维护、盘点、转移、报废等作业做合理的管制特订本程序。
二、范围 2.1 凡本公司自行设计开发的零组件所用的模具均属之。 2.2 ODM 所委托开发之模具均属之。
三、定义 ODM:即 OFFER DESIGN MANUFACTURE 委托设计制造之意。 落模保养 : 模具于生产中之每日例行保养 ,及下模后未达定期保养之规定所实施之保养 定期保养 : 生产模次到达规定的时间或模数 ,由模房所进行的保养 四、权责 4.1 工程部(模具课、生技课):负责模具设计开发、接收、验收、建档登录、定期保养、 落模保养、维修、协助工程变更修改模具等 。
成型课:负责模具保管、使用、落模保养、维护、盘点及报废等管理 。
品管课:协助模具验收 。
生管课:负责模具之转移及试模之安排 。
五、内容
5.2 新模具开发、采购、验收 重点模具的开发、采购、验收等主要由总公司进行相关作业。于本地之新开模具由工程 部主导 5.3 模具转移 因生产需要,相关单位拟将模具转移至厂,转移之相关工作由生管负责进行,模具转移 时需附〖射出成型记录表〗(附件 7.1)、〖模具评估报告〗(附件 7.2)、〖检验报 告〗(附件 7.3)及成品制作样品。若无上述资料可比照相关部品,“工程图面”验收模 具。 若为厂现地开模,则于模具验收时由模具课记录〖射出成型记录表〗(附件 7.4),并填 写 〖模具评估报告〗 (附件 7.5) 品管课检验部品并记录于 , 〖进料检验报告〗 (附件 7.6)。
模具课接到转移、新开或维修好的模具时,需先开模检查模具外观是否有伤痕及瑕疵, 若无瑕疵则填写〖试模通知单〗(附件 7.7),协调生管安排试模,并填写〖模具试模品质编号:EP05 程 序 文 件 模具管理作业程序 版本:A 页数:2/4确认单〗(附件 7.8),连同试模良品,送交品管、生技确认。确认完成后,转交成型课 生产。 若模具开模检查有瑕疵,则立即知会采购及相关单位,以便请厂商维修。 模具的试模及验收,由模具课主导,生技、品管、成型、生管等单位协助,验收完成后 方可转成型课进行量产。 模具接收 成型课接到新转移或维修好的模具后,将模具状况登录于〖模具基本资料明细表〗(附 件 7.9)上。
模具的保管与维护:
5.6.1 模具由模具房负责维修、落模保养与定期保养,成型课每月定期列出〖模具寿命 管制表〗(附件 7.10)对模具寿命进行管理。
5.6.2 模具于连续正常使用过程中,成型课每 24H 需对模具进行点检,并记录于〖模具 点检记录表〗(附件 7.11)。 若生产计划完成或暂停生产而下模时,由使用单位对模具进行全面清洗,并交模 具课进行落模保养。若模具已达定期保养之规定阶段 ,则模具课需进行定期保养
5.6.3 模具使用及保养完毕 ,由成型课人员负责将模具放入模具架上保管储存 落模保养 5.7.1 若生产计划完成或暂停生产而下模时,使用单位需将此模具最后一模之注塑品及 〖落模注铸品检查表〗(附件 7.12)连同模具,一起交给模具课进行落模保养。
5.7.2 模具课及品管课,先对落模品进行外观检视与尺寸检查,观看是否有外观缺失尺 寸异常及需整修之部位,若有则于此落模时一倂整修,若无则依下列清洗项目进 行落模保养及清理。
5.7.3 落模射出品之检视结果,由品管人员记录于〖落模注铸品检查表〗中,模具课人 员依不良项目填写维修内容, 维修完毕后交成型课进行试模, 并请品管人员确认。 修复后,〖落模注铸品检查表〗由成型,品管及模具课之主管签核,并保留修复 后之样品,以示修模确认与品质确认。
5.7.4 落模与修模之注塑样品,由成型课负责保存,并且随模具之上下模而更换,注塑 品或标示上,需注明保留之时间与型号等资料,以利追踪。
5.7.5 当对于样品之外观有不同意见时,由品保部主管决议判定。必要时由总经理或管 理代表决议。 落模保养清洗项目 :
5.7.6 必须用布对浇口套、主流道、分流道、进浇口进行清理,直到各部位无油污、 塑料及其它杂物为止,成型部分喷涂防锈剂。
5.7.7 用风枪把水道里残余水吹出水道。
5.7.8 模具存放时与摆放木架的接触面水咀一定要拆下。
5.7.9 对导柱、导套、滑块加注适量润滑脂,对顶针复位杆加注适量顶针油。
5.7.10 模具拆下后,送至模房做落模保养。 落模射出品之保管 模具定期保养 模具达定期保养之规定时,需由模具课进行定期保养,详细之保养时间与项目 ,请参照
〖模具定期保养记录表〗附件 7.13 之规定。保养完毕后,将结果记录于〖模具定期保养 记录表〗内。 保养内容 : 5.8.1 型腔部分检查
南昌市盛利达压铸厂
编号:EP05 程 序 文 件 模具管理作业程序 版本:A 页数:2/4
5.8.2 型腔部分清理
5.8.3 注射系统检查
5.8.4 注射系统清理
5.8.5 导向滑动部分检查
5.8.6 导向滑动部分清理
5.8.7 顶出系统检查
5.8.9 顶出系统清理
5.8.10 冷却系统检查
5.8.11 冷却系统清理
5.8.12 支撑系统检查
5.8.13 支撑系统清理
5.8.14 模芯检查
5.8.15 更换模芯
5.8.16 进胶点检查
5.8.17 更换进胶点
5.8.18 滑块检查、更换滑块
5.8.19 模仁检查、更换模仁
5.8.20 镶块检查、更换镶块 当模具达到原本之使用寿命时 ,除依落模保养之规定进行外观与尺寸检查之外 , 并对模 具进定期保养 . 若有异常经修复后 , 由工程与品保部门判定模具尚可使用 , 则此模具可继续使用 , 并 依定期保养之规定定期保养 . 落模保养结果填写于〖落模注铸品外观检查表〗, 定期保养填写于〖模具定期保养记录 表〗, 并皆需注明 “ 达使用寿命验证 “ 之字样 . 5.9 模具报废 模具达保证寿命期限 ,不堪使用或机种停产时,由成型课提出〖资产报废单〗(附件 7.14) 申请报废。 经工程、 品保、 生管单位会签确认后 ,送交总 经理核准 .必要时呈台北总 经 理核准 .并由模具房记录于〖机器/设备/治具履历表〗(附件 7.15)上 5.10 新模具开发 业务有需求或模具报废后需另开新模时 ,由生管课提出 〖模具需求申请表〗 (附件 7.16) , 经会签工程部及呈总 经理核准后进行新模具开发. 5.11 模具的盘点、转移 模具的盘点、转移,由成型课负责 ,并记录于〖模具基本资料明细表〗及模具清册内。 5.12 模具的维修 5.12.1 模具需维修时、由成型课填写〖模具维修处理单〗(附件 7.17),经部门主管同 意 ,并会签生管单位后 ,送交模具房维修模具 . 5.12.2 模具房依据〖模具维修处理单〗之内容维修模具 ,维修完成后将模具送回成型课 确认维修状况 ,以确认修模之结果是否符合需求 .若不符合需求需下模再次进 行修模 . 5.12.3 试模完后 ,请品保人员进行品质确认 . 5.12.4 确认无误后将部件及模具交回成型课 , 并于〖模具维修处理单〗上做结案 .另 维修之内容记录于〖机器/设备/治具履历表〗上。 5.13 模具的修改 5.13.1 若因生产效率、品质因素要求修改模具,由成型课提出修模需求. 5.13.2 若因模具设计变更, 由设计单位/ 营业单位或生技课发出 〖工程变更通知单〗 (附 件 7.18),由生技课依变更内容填写〖模、治工具制作(维修)委托单〗(附件
南昌市盛利达压铸厂
编号:EP05 程 序 文 件 模具管理作业程序 版本:A 页数:2/4
7.19)提出修模需求,模具课配合修改模具 5.13.3 修改完后由模房人员开立〖试模通知单〗请生管安排机台与时间试模。 5.13.4 试完模后 ,将修改品交给修改单位确认是否符合需求 , 若不符合需求需下模再 次进行修模 . 5.13.5 修改品确认无误后于量产前 ,需填写〖模具试模品质确认单〗,连同试模良品, 送交品管、生技确认。确认完成后才可转交成型课生产。
5.13.6 完成后于〖模、治工具制作(维修)委托单〗上做结案 .另维修之内容记录于 〖机器/设备/治具履历表〗上。
六、参考资料 无。 七、附件 7.1 〖射出成型记录表〗(样张) 7.2 〖模具评估报告〗(RE08) 7.3 〖检验报告〗(样张) 7.4 〖射出成型记录表〗(RT01) 7.5 〖模具评估报告〗(RE08) 7.6 〖进料检验报告〗(RQ01-1) 7.7 〖试模通知单〗(RT09) 7.8 〖模具试模品质确认单〗(RT08) 7.9 〖模具基本资料明细表〗(RE09) 7.10〖模具寿命管制表〗(RT05) 7.11〖模具点检记录表〗(RT06) 7.12〖落模注塑品检查表〗(RE37) 7.13〖模具定期保养记录表〗(RE36) 7.14〖资产/消耗品报废申请单〗(RE06) 7.15〖机器/设备/治具履历表〗(RE01) 7.16〖模具需求申请表〗(RE48) 7.17〖模具维修处理单〗(RT07) 7.18〖工程变更通知单〗(样张) 7.19〖模、治工具制作(维修)委托单〗(RE25)
压铸模具是铸造液态模锻的一种方法, 一种在专用的压铸模锻机上完成的工艺。它的基本工艺过程是:金属液先低速或高速铸造充型进模具的型腔内,模具有活动的型腔面,它随着金属液的冷却过程加压锻造,既消除毛坯的缩孔缩松缺陷,也使毛坯的内部组织达到锻态的破碎晶粒。毛坯的综合机械性能得到显著的提高。
压铸模具是铸造液态模锻的一种方法, 一种在专用的压铸模锻机上完成的工艺。它的基本工艺过程是:金属液先低速或高速铸造充型进模具的型腔内,模具有活动的型腔面,它随着金属液的冷却过程加压锻造,既消除毛坯的缩孔缩松缺陷,也使毛坯的内部组织达到锻态的破碎晶粒。毛坯的综合机械性能得到显著的提高。
7压铸模具三大产业难点
中国压铸[2]模具产业规模巨大,已雄居全球第二。但国产模具仅大量供应于国内,所以要进军国际市场,必须突破以下三个方面的制约:
一、我国压铸模具业在原材料的使用上面的不足。
二、技术的落后,使我国压铸模具产业的发展受到极大的阻碍。
三、我国压铸模具业的配套体系尚不充分。国内压铸模具只有加大研发力度,调整发展方式,解决以上三个方面的问题困扰,才能给在国外市场的竞争中获胜。
据了解,中国压铸模具行业发展迅速,总产量增长明显,国产压铸模具总产量仅次于美国,已经跃居世界第二位,成为名符其实的压铸大国。能有如此成就主要源于我国凭借着得天独厚的广阔市场以及相对低廉的资源与劳动力优势,已非常明显的性价比在国际压铸件贸易市场中占据着较大优势,很据形势来看,未来我国压铸行业发展前景十分广阔。
虽然我国的压铸模具在“十一五”期间有了重大的突破。但是其国际知名度排位仍然靠后,产量也日益攀升但是大多数压铸模具仅供于国内的需求。
此外,由于技术的制约使得质量难以突破,国内的一些大型需求企业也频频向国外的压铸模具企业伸出橄榄枝,严重的贸易逆差使得国内压铸企业举步维艰。
因此,我国压铸模具只有加大研发力度,调整发展方式,突破上述三个方面的难点,才能够进军国际市场并大获全胜。
8压铸模具产业发展的四大障碍
据了解,我国目前的压铸模具业的发展主要受制于以下几个因素:
一、原材料的使用上。
我国压铸模具业与国外的相比仍有许多不足。
二、制造技术的落后。
我国压铸模具产业的发展受到极大的阻碍,制造技术的落后已经成为压铸模具产业发展的一大瓶颈。
三、我国压铸模具业得配套体系不充分是其发展的又一大阻碍。
四、从总体上看,我国压铸模具企业的管理水平普遍较低,基本上没有好的规范,很多还是作坊式的管理,很多企业都是老板自己亲自管理,事无巨细全部由自己负责。这样的管理模式很大程度上限制了我国压铸模具企业的进一步发展。
我国经济的发展日进千里,已经初步建立起了一个完整的工业体系,这个庞大的工业体系的正常运行,离不开铸造模具产业的支持。据了解,截止目前为止,我国五金模具产业中仍然有百分之七十的企业为民营企业,而现下,我国正努力向着五金模具加工和出口大国的目标发展,要想取得良好的效果扩大五金模具市场和消费潜力一方面需要强硬的技术支撑,另一方面也需要高端大企的领军作用指导。
据统计,近年来我国每年用近10亿美元进口模具,其中精密、大型、复杂、长寿命模具占多数,所以从减少进口角度出发,这类高档模具,五金工具在市场的份额比例也将逐步增大。在未来的模具市场中中国制造模具会有重要的地位。
有了市场,我国的铸造模具产业形同在中国铸造模具产业内部装了一台功率极大的发动机,它将驱动我国的铸造模具产业不断的发展,将带领我国五金铸造模具产业更好的发展。并且五金模具的发展将会给模具整个行业带来转型期中最重要一个环节的飞跃,将会提速转型。