百科详情
发布时间:2022-04-02 09:54
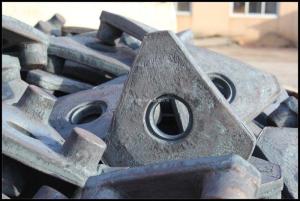
1特点
模锻件的特点应该是针对于自由锻来谈才会好一点,自由锻基本上不会有模具,只能锻轴、环等极其简单的东西,而模锻就可以锻出很多结构的产品,且可以控制产品的尺寸公差,减少车加工量。
2模锻件图
模锻件图是锻件图的一种,也有人简称为锻件图或毛坯图,除“锻件图”条中各项要求外,模锻件图绘制时由于本身特点还必须考虑:分模线位置;选定模锻斜度、决定冲孔连皮的型式;锻造工艺对锻件纤维方向的影响;机械性能试棒的位置;印记、钢号位置等。质量合格的锻件还必须具备下列要求:按锻造工艺规程锻制的锻件,其全部尺寸均应符合模锻件图上尺寸的要求,同时,必须满足模锻件图上所规定的技术条件要求,如热处理硬度、错移量大小、毛边痕大小、弯曲度、壁厚差、表面缺陷、除掉氧化皮及机械性能要求等。
曲轴锻压机用模锻件图:曲轴锻压机用模锻件图与制订锤上模锻件图的规则基本相同,但有以下三条特殊考虑因素:(1)锻压机具有顶杆装置,就可以立着锻造带长杆的锻件(即杆的轴线与滑块运动方向一致),以减少在分模面上锻件的周界,并减少毛边金属的消耗;(2)锻压机上模锻的锻件,它的余量的平均尺寸比锤上小30~50%,具体数字可查有关手册确定;(3)如靠手钳将锻件从模槽中取出的话,模锻斜度与锤上锻件一样确定,当采用顶杆将锻件顶出时,模锻斜度可显著地减小,但也不能完全没有,否则顶杆受负荷过大。
3模锻件分模面
分模面即锻模的上模与下模在锻件上的分界面,制定模锻件图时必须首先确定分模面,并考虑以下一些问题:(1)要保证锻件能自由地沿锤击方向从模槽中取出来。(2)分模的位置要尽量使模槽的深度最小和宽度最大,因为宽而浅的模槽是镦粗的方式充满的,狭而深的模槽是压入的方式充满的,后者金属充满要困难些,模槽磨损量相对要大些。(3)分模面应尽量使上下两部分对称。上下模的形状尽可能一样,避免使分模面选择在端面上,以利于错移时及时发现。(4)为简化模子制造,分模面应尽量做成平面,而不是曲面,但第二类锻件有时还必须选择曲面分模。(5)锻件较复杂部分尽量安排在上模内,因为上模内金属容易充满模槽。以上各项要综合考虑,以达到正确而又合理地选择分模面位置。
4锻模
模锻时,使用的模具,称为锻模。从金属开始变形到最终成形,都是利用锻模的相应模膛进行的。锻模分上下锻模,分别安装于锤头和砧座上,借助于燕尾和键槽的作用,防止锻模脱出、松动、左右横向移动,并用键块、楔铁将其紧固在锤头燕尾槽内和砧座燕尾槽内,防止锻模前后纵向移动。上下模用锤楔的偏斜方向是不同的,而键块的小头位于锻模燕尾的键槽内,大头位于锤头或模座的燕尾槽的键槽内。锻模在工作过程中不断地承受冲击力作用,所以锻模工作前必须预热到150~200℃左右,以免温差产生的应力经重击造成锻模破裂,锻模的型式有整体锻模和镶块锻模两种,以前者居多,当模槽的个别部分(模槽的凸起部分)容易磨损时可把易损部分作成可拆换的镶块,组成局部镶块锻模,镶块装配一般采用热压及楔铁紧固两种方法,前者多适用于局部镶块装配。为平衡曲面分模面产生的分力,在锻模上设置平衡制动扣,防止锻模错移。锻模制动扣(导轨或销扣)有多种形式:圆形的、对角的、四角的等,在锻模模槽靠近操作方向的一端留有钳口,便于夹持毛坯用,夹钳在工作时位于这个空间里。为了便于锻模安装和调整,在锻模的两个相邻侧面靠近分模的地方刨去高为30~50毫米、深为5毫米的一段形成检验角。锻模工作时要注意冷却和润滑,常见冷却剂是压缩空气、食盐饱和溶液、锯末拌有少量冷水等。常见润滑剂是食盐水、锯末以及炮油、二硫化钼等。
5模锻件的公差和加工余量
在模锻过程中,由于坯料在高温条件下产生表皮氧化、脱碳现象,导致锻件表面质量不佳,甚至产生其他缺陷;由于坯料体积变化及终锻温度波动,使锻件尺寸控制不定;由于锻件出模的需要使锻件侧壁添加敷料;由于型槽磨损和上、下模难免的错移现象,导致锻件尺寸出现偏差等。所有这些原因使锻件不仅应有机械加工余量,而且还要规定适当的锻件尺寸公差。
锻件的各种尺寸和公差余量锻件上需要机械加工的部位,都应给予加工余量。此外,一些重要的承力件,要求100%取样试验或者为了检验与机械加工定位的需要,还应给予必须的工艺余块。
在实际模锻生产中,由于受到各种工艺因素的影响,锻件的实际尺寸不可能与公称尺寸相等,无论在高度方向还是水平方向尺寸都会有偏差,因此对锻件规定允许有一定限度的偏差范围。锻件最大尺寸大于锻件公称尺寸的部分为正公差,锻件最小尺寸小于锻件公称尺寸为负公差,如图所示。
有关钢制模锻件的工差及机械加工余量,可参考GB/T12362-2016。[1]